熔模鑄造缺陷
當前的熔模鑄造企業,尤其是中小企業的技術人員嚴重缺失、斷層;對減少、預防熔模鑄造缺陷缺少思路、缺少方法、缺少經驗;已經嚴重的制約了企業的競爭力、效率和效益,成為企業發展的瓶頸。
蠟模(也稱“熔模”)制作是生產中的第一道、也是重要的一道工序,是獲得優質鑄件的首要條件。蠟模產生缺陷,浪費了制模的人工費用、生產時間和有效的資源;不合格的蠟模流入制殼工序,甚至澆注工序,產生了不良品。會增加工廠的生產成本、交貨期,影響企業的信譽和經濟效益。因此,應重視和解決蠟模缺陷。
壓制熔模是用模料經過配置、壓制、冷卻、修模和組焊等工序組成,如圖1:
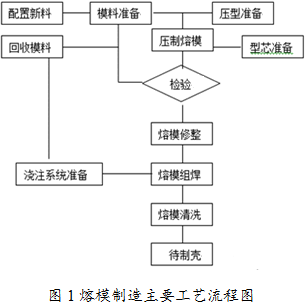
當前,壓制蠟模廣泛使用蠟基低溫模料,或中溫蠟料(如K521)。一般情況下,蠟模存在氣孔、縮陷和裂紋等13種缺陷?,F分述如下:
一、氣孔
1.缺陷特征
蠟模的局部表面上,留有表面光滑的氣穴,如圖2所示。
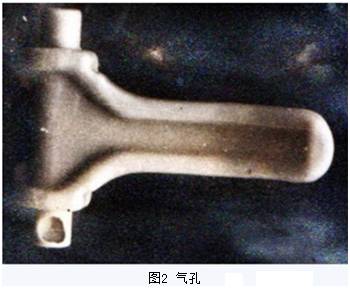
2.產生原因
(1)配置蠟料卷入過多的氣體,沒有充分回性處理。
生產中,配置低溫蠟料常采用化蠟、刨蠟片、攪蠟膏和回性四個工序,常選用螺旋式葉片攪拌機攪拌蠟料(或“蠟膏”)。在攪拌蠟料的過程中,不可避免地卷入很多氣體;并且隨著攪拌機轉數的增加,卷入的氣體越多。尤其是蠟料攪拌后,沒有進行充分的回性處理,使卷入的大量氣體從蠟料中溢出,而是仍然殘留在蠟料中。
(2)注蠟孔的位置不當,注蠟過程中卷入氣體。
注蠟孔的位置設置不當,使蠟料在注入型腔的過程中產生渦流,卷入了過多的氣體。
(3)壓型設計不當,不利于型腔排氣。
蠟料充滿型腔的距離太長,并且型腔排氣不良。
3.防止措施
(1)嚴格遵守蠟料配置工藝和操作規程。
配置石蠟—硬脂酸蠟料時,注意加料順序,即先加硬脂酸,待其全部熔化后再加入石蠟或回收蠟,加熱至全熔狀態,其溫度≤90℃。開始攪拌時,攪拌機的轉數可以高些(如400r/min),蠟料溫度升高后,可以降低攪拌機的轉數(200~300r/min)。蠟料攪拌合適后,要進行回性處理,時間在0.5h以上,使卷入蠟料中的氣體充分溢出。
(2)改進注蠟孔的位置,避免蠟料在型腔中產生紊流。
注蠟口最好設置在內澆道或有加工余量的表面上,尺寸應與壓蠟機的注蠟嘴匹配;注蠟口應確保蠟料以最短的距離、平穩充滿型腔,并且不產生紊流。
(3)改進壓型設計,以利于排出型腔中的氣體。
改進壓型的設計,有利于排出型腔中的氣體;必要時增設排氣孔。
二、縮陷
1.缺陷特征
蠟模肥厚處出現局部收縮產生的凹陷,如圖3所示。
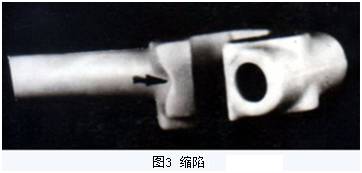
2.產生原因
(1)蠟模的厚大處(凹陷處)補縮不足。
蠟模的注射壓力是制模工藝的主要參數之一。注射壓力小使蠟模的厚大處(凹陷處)的收縮率大,當得不到充分的補縮時,該處產生縮陷。
保壓時間是制模工藝的另一個工藝參數。蠟料充滿壓型型腔后,保壓的時間不足,使蠟模的厚大處(凹陷處)的收縮率加大,當得不到充分的補時,造成該處蠟??s陷。
(2)蠟模的注入量不足,補縮不充分。
注蠟孔小,或位置不當,或注蠟的壓力小時,注入壓型型腔的蠟料量不足,當蠟模厚大處(凹陷處)得不到充分的補縮時,造成該處蠟??s陷。
(3)蠟模的壁厚差過大,不利于補縮。
蠟模的結構設計的不合理,壁厚差過大,不利于補縮。
(4)注蠟時蠟料的溫度過高,或壓型的溫度過高,或兩者都高。
蠟料溫度高,或壓型溫度高,或兩者都高,使蠟料的收縮率增大;當得不到充分的補縮時,而產生縮陷。
(5)蠟料的收縮率較大。
生產中使用石蠟-硬脂酸蠟料,常用58~62℃(即58號~62號)白石蠟和一級三壓硬脂酸,新配置料時,各占50%。58號白石蠟的收縮率就大于62號白石蠟。石蠟-硬脂酸蠟料比石蠟-低分子聚乙烯蠟料的收縮率大。
3.防止措施
(1)增加蠟料的補縮能力。
壓制蠟模時,注射壓力一般選用0.2~0.5MPa。適當的提高注射壓力不僅增加壓型中蠟料的密度,而且可以降低蠟料的收縮率。適當的增加保壓時間,一般選用(3~10)s或更長;同樣可以減少蠟料的收縮率,增加蠟料的補縮能力。
(2)加大蠟料的注入量,增加補縮能力。
適當的加大注蠟孔的截面,增加單位時間內的蠟料注入量;或改變注蠟孔的位置,使蠟模的壁厚處得到充分的補縮。
(3)改進蠟模結構使其壁厚盡量均勻。
在可能的情況下,盡量使蠟模的壁厚均勻;必要時,在蠟模的肥厚處放置預先制好的冷蠟塊(也稱“蠟芯”),再注入蠟料形成蠟模。應根據蠟模的大小和形狀,可以局部或整體放置冷蠟塊。冷蠟塊應該用錐形的凸臺在壓型中定位。凸臺的高度應該根據零件的大小予以確定,一般控制在2~3mm。冷蠟塊使用的蠟料應與蠟模的蠟料一致。
(4)注蠟時,控制蠟料和壓型的溫度。
注蠟時,對于低溫蠟料一般選用蠟料溫度T=48~52℃,壓型的溫度T=18~25℃為宜;對于中溫蠟料一般選用蠟料溫度T=52~60℃,壓型的溫度T=20~24℃為宜。
(5)選用收縮率較小的蠟料。
如當選用62℃白石蠟代替58℃白石蠟時,減少其收縮率?;蛱岣呦灹现惺灥暮?~10%,即55~60%,也可減少蠟料的收縮率?;虿捎?0℃白石蠟(含量95%)與低分子聚乙烯(含量5%)配制的蠟料,其收縮率約為1%,較低。
三、裂紋
1.缺陷特征
蠟模局部裂紋,常出現在蠟模的分型面,如圖4所示。
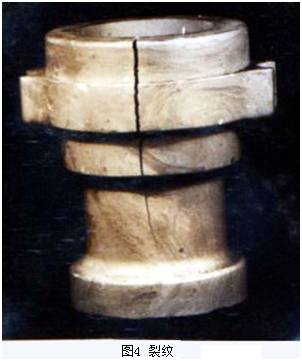
2.產生原因
(1)蠟料的收縮率大,塑性差。
采用58℃精白蠟或白石蠟與一級三壓硬脂酸按照各50%配制蠟料時,蠟模的自由收縮率約為2%。當蠟料中硬脂酸的含量大于80%時,其韌性、塑性都差。易引起蠟模產生裂紋。
(2)壓型,或制模間,或冷卻水的溫度過低。
壓型的溫度過低,或制模間的溫度過低,或冷卻水的溫度過低,導致蠟模冷卻過快,當蠟模收縮受阻時,易產生裂紋;或蠟模在壓型中冷卻的時間過長(即起模時間過長),導致蠟模收縮受阻時,易產生裂紋。
(3)蠟模結構/壓型設計不合理。
蠟模結構/壓型設計不合理,蠟模的壁厚不均勻,厚薄過度部分的圓角太小或呈尖角,當蠟模收縮受阻時,在其薄弱部位產生裂紋。
(4)操作不當。
起模方法不當,或抽取芯棒的時間太晚,造成蠟模產生裂紋。
3.防止措施
(1)選用收縮率較小的蠟料。
對于低溫蠟料,當選用62℃白石蠟代替58℃白石蠟時,可以減少其收縮率?;蛱岣呦灹现惺灥暮?~10%,即55~60%,也可減少蠟料的收縮率?;虿捎?0℃白石蠟(含量95%)與低分子聚乙烯(含量5%)配制的蠟料,其收縮率約為1%,較低。
(2)控制壓型、制模間和冷卻水的溫度。
對于低溫蠟料壓型的溫度控制在18~25℃,中溫蠟料壓型的溫度控制在20~24℃為宜。制模間的溫度應控制與壓型溫度一致,冷卻水的溫度也應控制與室溫一致;必要時制模間應安裝空調,溫度控制在20℃為宜。
(3)改進蠟模設計(即壓型設計)。
改進蠟模設計,盡量使其壁厚均勻;壁厚不均勻應圓角過度(過度圓角應為“兩個相鄰壁厚之和”)的“1/5~1/3”);必要時可以增加工藝筋,把蠟模收縮時的應力降到不產生裂紋的程度。
(4)嚴格執行操作規程。
改進起模方法,必要時增加起模裝置,避免蠟模在起模過程中產生裂紋。
嚴格控制蠟模冷卻時間,一般為10~60min。蠟模冷卻后應及時取出隨蠟模一起冷卻的芯棒,使其不能阻礙蠟模的收縮。
——本信息摘自網絡未經證實,僅供參考